Michelle Kruger: Austal USA President
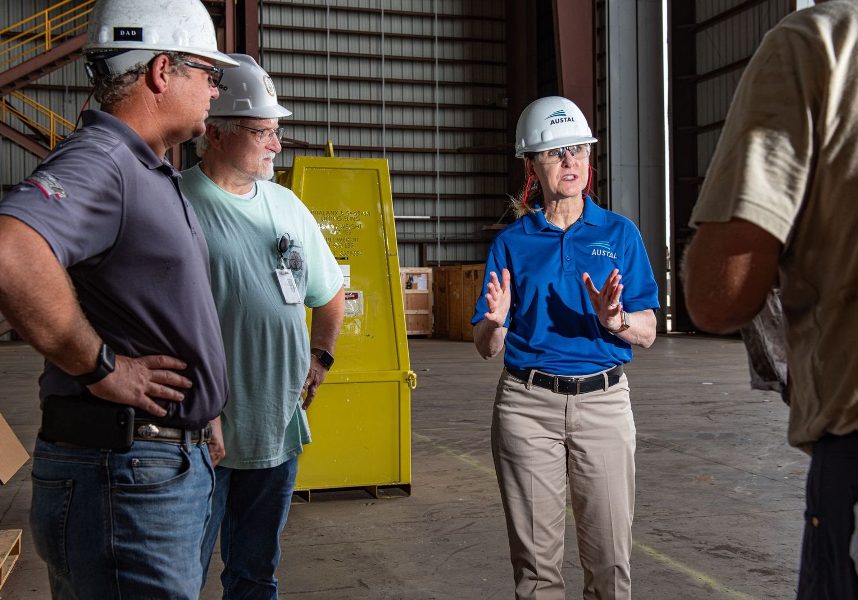
On leading “a positive, transformational force in the maritime industry”
By Angie C. Baldwin
photography by Stephen Savage, assisted by Holly McKinney and Kevin Zhou of Chromatic Creative, LLC.
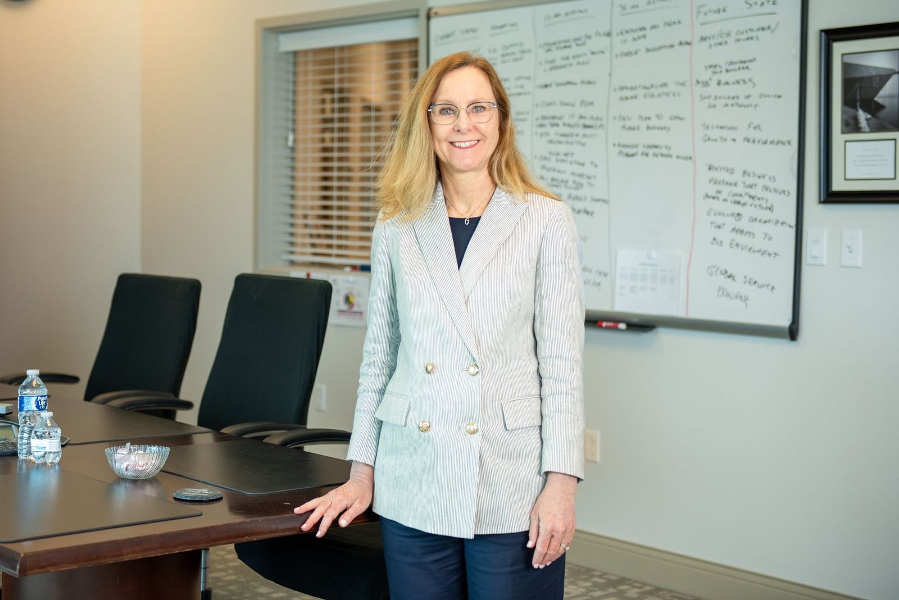
Austal USA President Michelle Kruger (MK), a Canton, Ohio, native, calls sailing and connecting with nature lifelong passions. She began sailing with her parents and sister as a young child, and the sport took on greater meaning when her blue-collar, hard-working parents fulfilled their dream of sailing around the world. She says their journey etched a profound lesson – “dreams, no matter how audacious, are achievable with unwavering commitment and hard work.” This core value has shaped who she is and the path she’s taken, from her time as a student at the U.S. Merchant Marine Academy (USMMA) to her decorated career as a marine engineer, and the last two years with Austal USA. In her fairly new role as president, she is executing plans to ensure the shipbuilding company’s future growth and success.
AB: What inspired you to attend USMMA?
MK: My journey to USMMA began with my sister, Diana, a proud 1984 alumna. A family visit to Kings Point, NY, opened my eyes to the Academy’s unique blend of academics, regimented life and exciting career paths – not to mention the opportunity to travel the world.
From the demanding academic curriculum to the deep sense of camaraderie, every aspect – the cultural immersion, the instilled discipline – played a vital role. “Acta Non Verba” (Actions, Not Words) isn’t just a motto; it’s a guiding principle I carry with me. During my junior year at sea, my parents, true to their word, made a life-changing decision: They sold our home. Facing this independence, USMMA became my anchor, fostering personal growth and a smooth transition into adulthood.
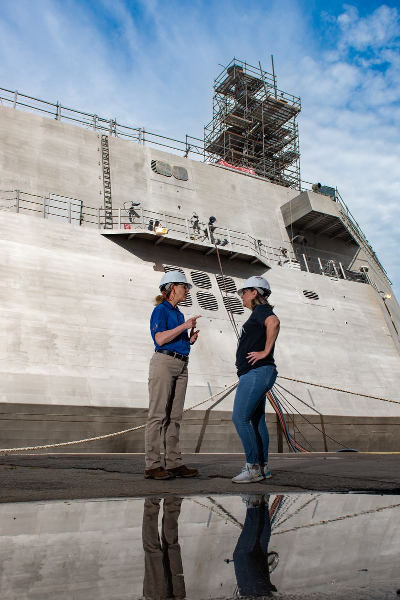
AB: How did those years inform your future career?
MK: USMMA provided the bedrock for my career in the maritime industry. My foundation in engineering and leadership proved invaluable in shipbuilding, repair and maintenance. While I took a detour to open a winery and bed and breakfast in North Stonington, Conn., the maritime world always called me back. This experience, however, instilled in me valuable skills in entrepreneurship and hospitality that I’ve been able to leverage throughout my career.
AB: Can you share some highlights and personal achievements from your career as a marine engineer?
MK: Joining the team at General Dynamics National Steel and Shipbuilding Company (NASSCO), I was determined to transform them from a “windsock” (reacting to external forces) to the “engine” driving the company’s success. This involved fostering a learning culture where everyone’s ideas were valued, implemented and celebrated. We embarked on an effort to benchmark best-in-industry practices and bring them to NASSCO to identify and eliminate production inefficiencies. This empowered our team to continuously improve and accelerate production.
As the capture manager, leading the team to secure the Littoral Combat Ship (LCS) sustainment contract was a defining moment. What truly excited me was exceeding expectations – not just winning, but also establishing the program infrastructure (both CONUS [continental U.S.] and OCONUS [outside the continental U.S.]) from scratch. This victory showcased the power of collaboration and teamwork.
“Austal USA is poised for significant growth, and
– Austal USA President Michelle Kruger
our infrastructure expansion plans reflect this
commitment.”
My entire maritime journey has been a source of immense pride. I learned important lessons at each shipyard: rigorous process discipline and strict accountability; the transformative power of an empowered, learning workforce and the importance of company culture.
At Austal USA, we have a phenomenal workforce – the best in the nation. Together, we’re a positive, transformational force in the maritime industry, constantly innovating, evolving and delivering high-quality ships, maintenance and technology.
AB: What are some of the challenges you’ve faced and overcome along the way?
MK: A recurring challenge throughout my career has been navigating transitions between departments and companies. Each move presented the hurdle of gaining the confidence and trust of my team, leadership and customers.
My approach focused on establishing mutual trust in each new environment. This involved actively listening to understand concerns, demonstrating competence through results and fostering open communication. Once trust was built, it had a ripple effect, extending to colleagues and clients alike. This collaborative environment ultimately led to unbridled performance, exceeding expectations across the board.
AB: What led you to Austal USA in 2022? What about the company appeals to you?
MK: In 2022, I was approached about the position running the services business. After a tour of the Austal USA facility and meeting the team, I recognized I had an opportunity to join a great team. There was an undeniable energy – a palpable sense of pride, passion, innovation and grit. This infectious enthusiasm was unlike anything I’d experienced before.
The Austal USA culture truly captivated me, and it sparked a fire within me. Ultimately, it led me to make the difficult decision to step away from NASSCO and join the Austal USA team. It’s a decision I haven’t regretted for a single moment.
AB: You quickly transitioned from vice president of global services and support to interim president to president. Can you talk a little bit about how the past two years at Austal USA have been for you and how you are settling into your role as president?
MK: These past two years have been energizing and rewarding. I could not have predicted this outcome and am honored to have been appointed Austal USA’s president.
I was hired as the vice president of Global Services and Support in 2022. In that role, the following year I had the privilege and unique opportunity to take over a recently acquired waterfront facility and build a repair facility on the San Diego waterfront, christening our new yard with an availability for the USS Canberra (LCS 30).
We have a strong leadership team, and our new construction portfolio is the most diverse it has ever been. We are a growing force in the shipbuilding and ship repair industry, building ships for the U.S. Navy and the U.S. Coast Guard, building submarine modules for the Columbia and Virginia class programs, elevators for the Ford-class aircraft carriers, and unmanned ships. We started construction on the U.S. Navy LCU (Landing Craft Utility) Program and have delivered two ships since I was appointed interim president in August 2023. We also christened LCS 38, the future USS Pierre, the last LCS.
One of the most rewarding events was meeting our entire workforce during our October 2023 all-hands meeting. I’m so proud of each person and their contribution to Austal USA, and their commitment to being the safest, most agile, mission-focused team in the industry. Similarly, our community leadership, engagement and support are priceless. Austal USA would not be successful without the partnership we share. I am thrilled to continue fostering our relationship for decades to come.
AB: What are some of your goals as president of Austal USA?
MK: I am constantly inspired by the skill, dedication and adaptability of our incredible team – women and men who are the backbone of Austal USA. My goal is to further enhance their expertise and make Austal USA the premier surface shipbuilder and submarine module manufacturer in the nation.
We are committed to delivering world-class service and support across the globe. We will also focus on steadily advancing technology to ensure our solutions meet the ever-evolving needs of our nation’s defense.
By achieving these goals, Austal USA will become one of the most reliable, versatile and trusted partners in the maritime industry. We are dedicated to supporting the successful implementation of the National Defense Industrial Strategy.
AB: The economy has had its challenges over the past few years, with inflation, supply chain issues and an ongoing shortage of skilled labor. Have these issues impacted Austal USA? If so, how has Austal USA dealt with them?
MK: Like many in the industry, Austal USA has faced recent economic challenges – inflation, supply chain disruptions and a skilled labor shortage. However, we’ve taken a proactive approach to overcome these hurdles.
We’ve strategically developed strong relationships with suppliers across 47 states. The LCS program itself has fostered a network of more than 28,000 suppliers. This robust network provides a solid foundation and helps mitigate supply chain disruptions.
Recognizing the skilled labor shortage, we’re heavily invested in workforce development. This includes:
- Community Collaboration: We recently hosted our first workforce-development roundtable with local educators. This collaborative effort paves the way for attracting and training the next generation of shipbuilders.
- Increased Workforce: With a focus on growth, we plan to expand our current workforce of 3,000 to more than 4,500 in the coming years.
Austal USA is committed to supporting national security initiatives. We were recently called upon by the Submarine Industrial Base to accelerate submarine construction. To achieve this critical goal, we’re actively recruiting and training a skilled workforce capable of building both surface ships and submarine modules.
We understand the importance of strong partnerships. We work closely with the U.S. Navy, Marine Corps and Coast Guard to develop and implement solutions that ensure our collective success. In today’s environment, collaborative efforts are more crucial than ever.
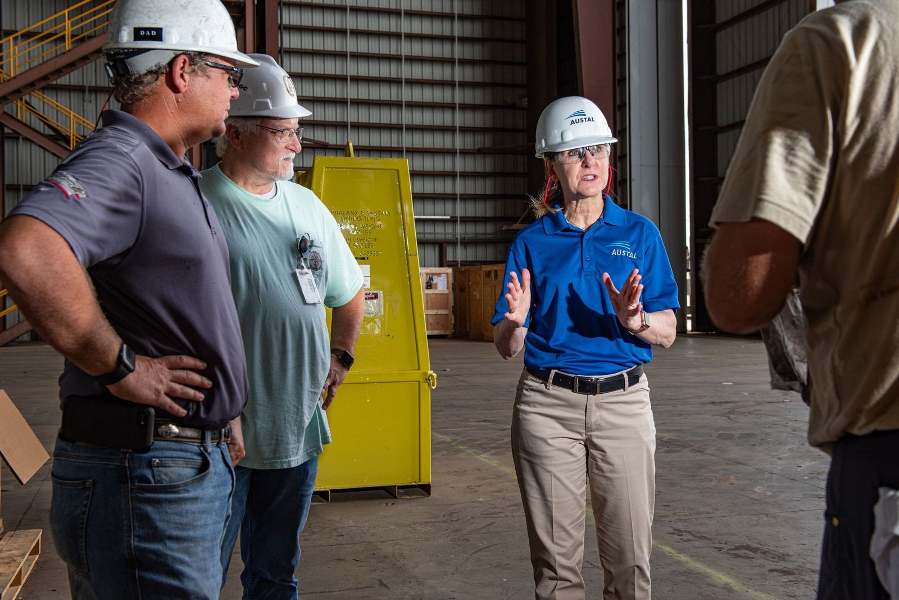
AB: What does the future hold for Austal USA?
MK: Austal USA is poised for significant growth, and our infrastructure expansion plans reflect this commitment. We’re currently designing two key projects:
- Final Assembly 2 (FA2): This project, announced in February 2024, will add three new assembly bays, waterfront improvements and a shiplift system. This expansion allows us to assemble larger steel modules. It also provides additional space to erect completed modules manufactured in our existing facilities. With FA2, we’re well-positioned to execute projects like Offshore Patrol Cutters, TAGOS surveillance ships and, potentially, frigates. Construction is expected to start in July 2024, with an investment of approximately $250 million.
- Module Manufacturing Facility 3 (MMF3): This state-of-the-art facility is specifically designed for submarine module manufacturing, supporting both Columbia and Virginia-class submarines. It will be the first Industry 4.0 facility for the U.S. Navy, leveraging advanced technologies to optimize production.
Upon completion of these projects, the Austal USA Mobile facility will boast:
- 180 acres: Offering ample space for future growth.
- 1.5 million square feet of indoor manufacturing space: Providing significant production capacity.
- 117,000-square-foot steel panel line: Dedicated to high-quality steel fabrication.
- More than 1 million square feet of covered module manufacturing space across two module manufacturing facilities.
- Seven assembly bays: Allowing for efficient module erection and final ship construction.
These expansions will significantly enhance our capabilities, enabling us to deliver larger, more complex vessels for the U.S. Navy and Coast Guard and other customers. Furthermore, MMF3 positions Austal USA as a leader in submarine module manufacturing, supporting critical national defense needs.
AB: How does Austal USA anticipate answering the challenge of the diversity of contracts it’s been awarded over the past couple of years?
MK: The variety of contracts Austal USA has secured – steel, aluminum, unmanned vessels, etc. – presents a unique challenge. However, we view this as an opportunity to showcase our versatility and adaptability. We’re tackling this challenge through:
- Comprehensive Review: We are conducting a thorough analysis of our entire organization, encompassing structure, processes and tools. No aspect will be overlooked.
- Process Optimization: This review will identify areas for improvement in our processes to ensure they efficiently accommodate diverse projects.
- Tool Investment: We will invest in the necessary tools and technologies required to handle the specific demands of each contract.
- Skilled Workforce: We are committed to fostering a highly skilled workforce with the expertise and flexibility to adapt to diverse projects.
This multi-faceted approach will ensure Austal USA is well-equipped to handle the current and future diversity of our contracts. We are confident in our ability to overcome any challenge and deliver exceptional results for our customers
Read More
- « Previous
- 1
- 2
- 3
- 4
- Next »
Subscribe to our weekly newsletter
Sign up here for free to get Bay Business News email newsletter every Friday.
By subscribing, you agree to our User Agreement and Privacy Policy & Cookie Statement.